Expansion of Inpro’s Quality Department: process optimisation and continuous improvement
At Inpro, we have always been committed to offering products and services of the highest quality. With the expansion of the Quality Department, we reaffirm our commitment to customer satisfaction and continuous improvement.
Our team of quality experts work tirelessly to ensure that every product and service we offer meets the highest standards. From design to shipment, every step of the process is subject to rigorous quality controls to ensure reliability, durability and performance. At Inpro, we are confident that these improvements will further strengthen our relationship with our valued customers by maintaining and improving product and service quality and regulatory compliance.
Improvements in our manufacturing process
Thanks to the improvements implemented in the manufacturing processes and the Quality Department, we have significantly optimised delivery times, as well as significantly reduced product returns and repairs. At Inpro, we strive to provide an exceptional customer experience, and these improvements are a sign of our continued commitment to evolution in all aspects of our service.
INPRO is committed to the quality of the products it manufactures to guarantee the maximum satisfaction of our customers.
Key benefits of Inpro’s Quality Department
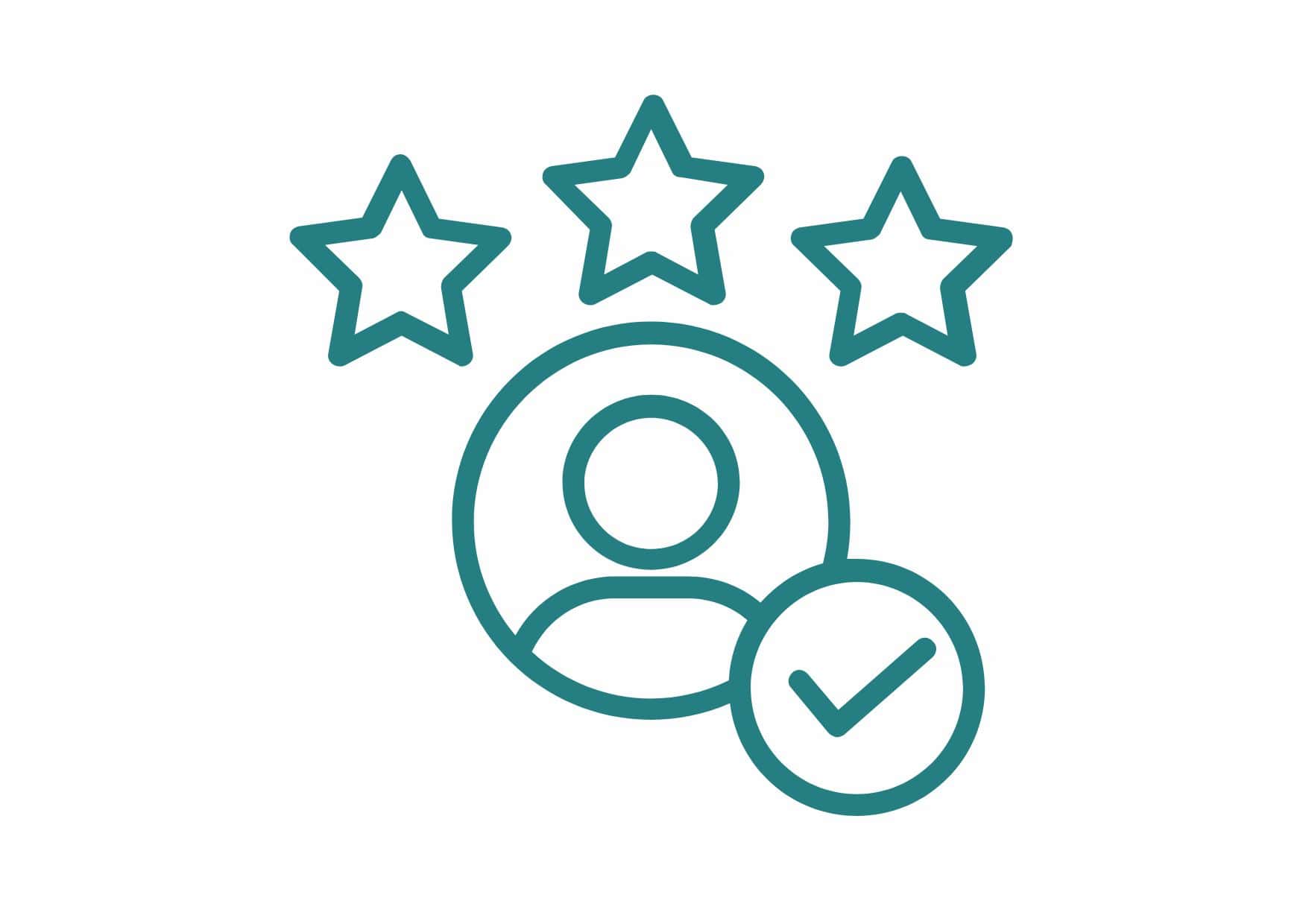
1. Compliance with standards and regulations: To ensure that all our Inpro products and services meet internal and external quality standards, as well as relevant industry standards and regulations.
2. Improved repairs: By identifying and addressing quality issues early in the process, the number of defective or unsatisfactory products will be reduced, which in turn will reduce the costs associated with rework, returns and warranties.
3. Improving customer satisfaction: Delivering high quality products and services will increase customer satisfaction, which can lead to increased loyalty, positive recommendations.
4. Increased operational efficiency: Al implementar procesos de control de calidad efectivos, se pueden identificar y eliminar cuellos de botella, reducir el tiempo de inactividad y optimizar la eficiencia en toda la cadena de producción.
5. Continuous innovation: Para fomentar una cultura de mejora continua, donde se busquen constantemente nuevas formas de mejorar la calidad y la eficiencia en todos los aspectos de nuestra empresa.
6. Reduced delivery times: Through careful optimisation of our logistics processes and increased coordination across the supply chain. We are committed to continuing to improve and adapt to meet the changing needs of our customers.
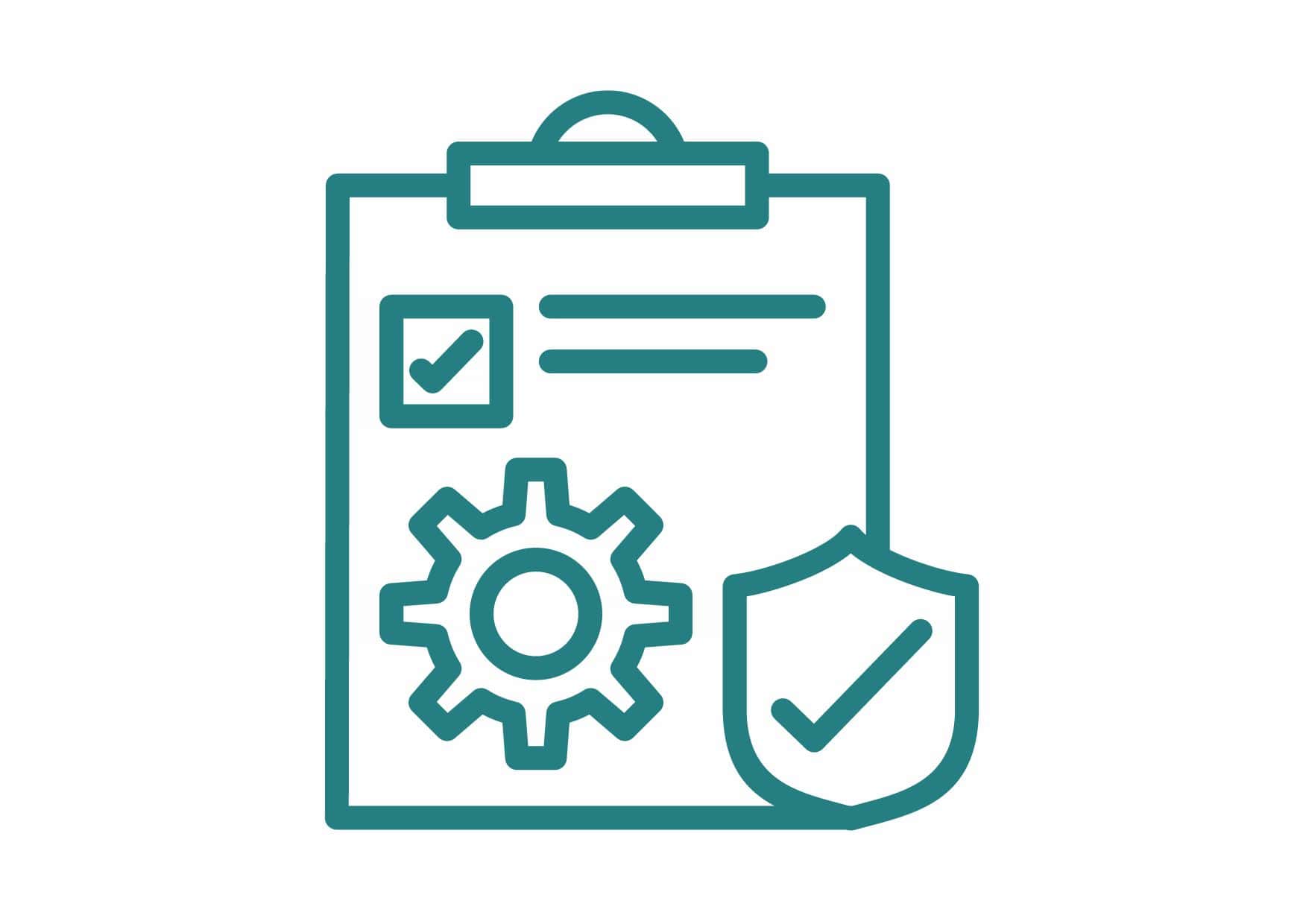
INPRO has a Quality Management System based on the UNE-EN-ISO 9001: 2015 standard
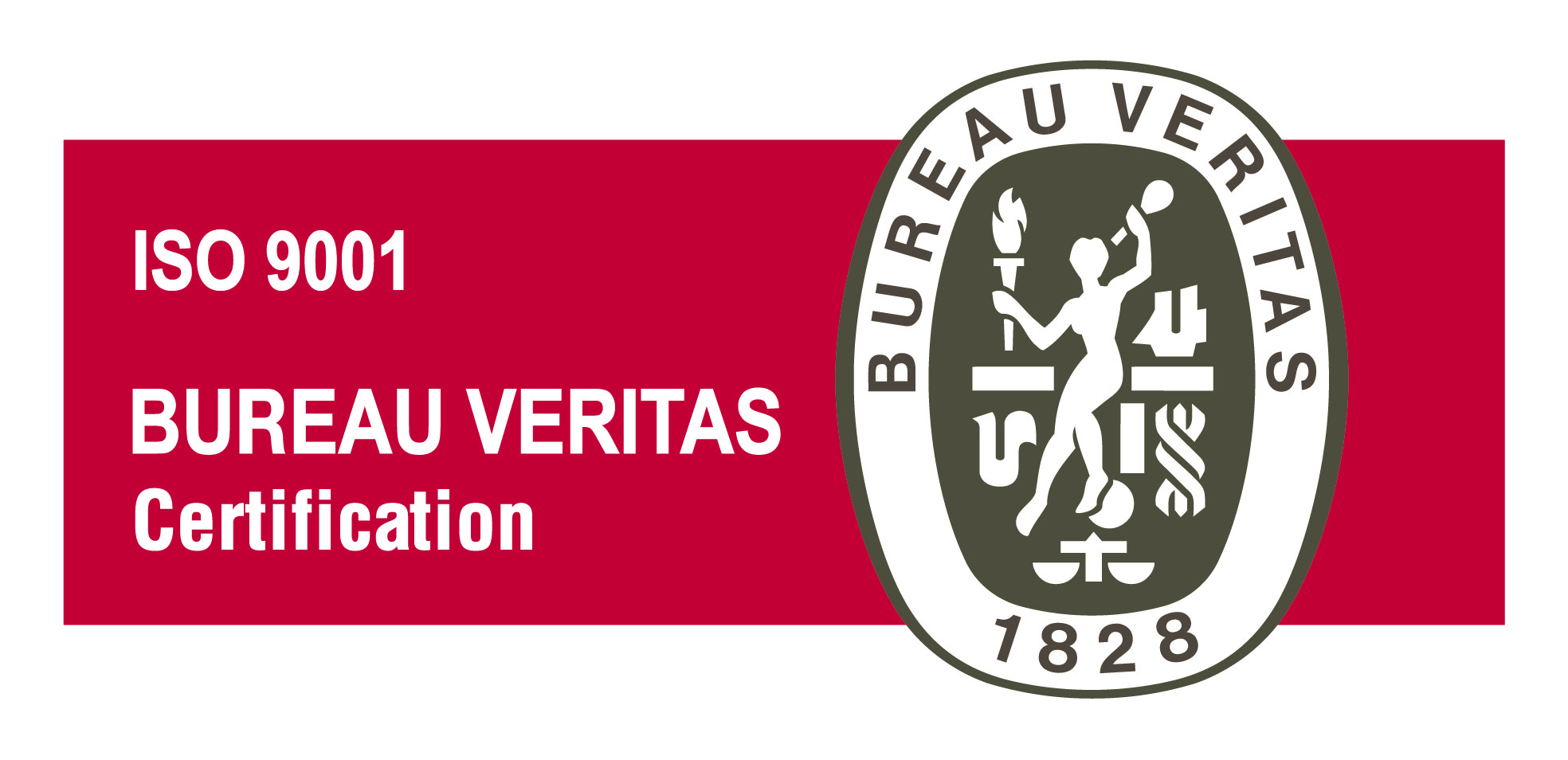
Reincorporation of Antonio Santamaría as Quality Manager
In his new role, Antonio Santamaria will be responsible for overseeing and leading all quality-related initiatives at Inpro. He will bring his extensive experience to further strengthen our focus on quality and continuous improvement.
Information about our services
For more information about our products, services and projects, please send an e-mail to info@inprord.com or fill in the following form: